As an indispensable means of vertical transportation in modern buildings, the production process of elevators involves a variety of professional equipment. This article will introduce the key equipment in elevator production in detail and explore their role in the manufacturing process.

What are the Types of Elevators?
Usage Classification:
- Passenger elevator: Designed for transporting passengers, with complete safety facilities and decorations, widely used in office buildings, shopping malls and residential places.
- Cargo elevator: Mainly used for transporting goods, usually with a large load capacity, suitable for factories, warehouses and other places.
- Medical elevator: Designed for transporting beds and medical equipment, the car is usually long and narrow to accommodate beds.
- Sightseeing elevator: The car is made of transparent materials, and passengers can enjoy the external landscape during the ride. It is often used in high-end hotels and tourist attractions.
- Home elevator: A small elevator designed for private residences, usually with a small load, and more attention to personalization and comfort.
- Hydraulic elevator: Driven by a hydraulic system, suitable for places with limited space, and does not require a traditional machine room.
- Machine roomless elevator: The control equipment and drive machinery are integrated in the shaft, saving space, suitable for modern high-rise buildings.
- Car elevator: Designed for transporting cars, commonly used in 4S stores and large parking lots.
- Miscellaneous elevator: Used to transport small goods such as documents and food, and does not allow people.
- Construction elevator: Used for vertical transportation at construction sites.
By Operating Speed:
- Low speed elevator: The speed is usually no more than 1.0 m/s.
- Medium speed elevator: The speed is between 1.0 m/s and 2.0 m/s.
- High speed elevator: The speed is more than 2.0 m/s.
- Ultra high speed elevator: The speed can reach 5.0 m/s and above, and is used in high-rise buildings such as skyscrapers.
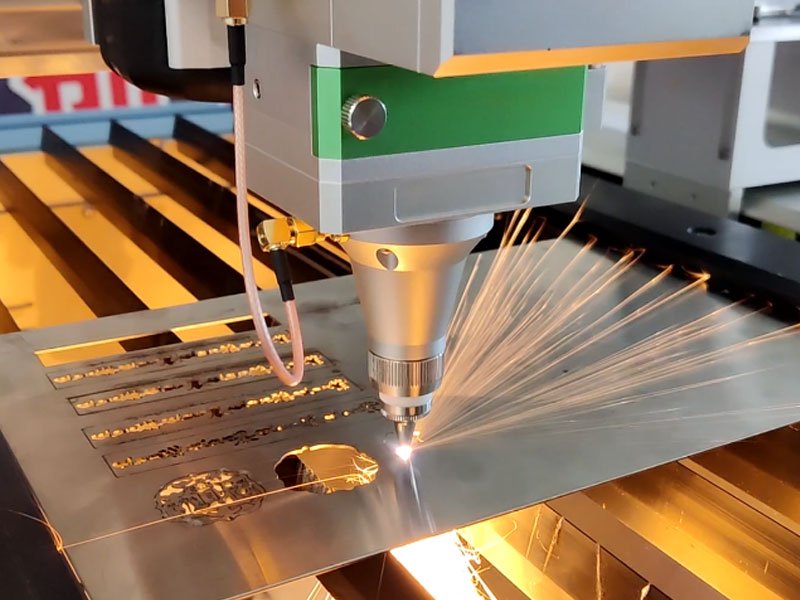
Advantages of Laser Cutting Elevators:
- High precision: Laser cutting machines can achieve precise cutting of complex graphics and reduce material waste.
- Fast processing: Compared with traditional mechanical cutting, laser cutting is faster and improves production efficiency.
- Contactless cutting: The laser head does not contact the material surface, avoiding physical damage and deformation.
- Strong flexibility: Able to handle materials of various thicknesses and shapes to meet different elevator design requirements.
Which Materials Are Best Suited for Laser Cutting in Elevator Manufacturing?
Stainless Steel:
Stainless steel is one of the most commonly used materials in elevator manufacturing, especially in the outer shell of elevator cars and doors. Laser cutting can handle stainless steel with a thickness of 1-12mm, and the surface after cutting is smooth and burr-free, suitable for high-standard appearance requirements.
Aluminum Alloy:
Aluminum alloy is also widely used in elevator components due to its lightness and corrosion resistance. Laser cutting machines can effectively cut aluminum plates with a thickness of up to 8mm, ensuring precise cutting and good surface quality.
Carbon Steel:
Laser cutting machines also perform well for low-carbon steel with a thickness of 8-20mm. This type of material is often used in the structural part of the elevator, and laser cutting can complete large-scale production quickly and efficiently.
Plastics and composites:
Although not often used in the main structure of the elevator, laser cutting can also handle plastics (such as polymers) and composites on certain decorative or functional parts, especially when these materials require complex shapes.
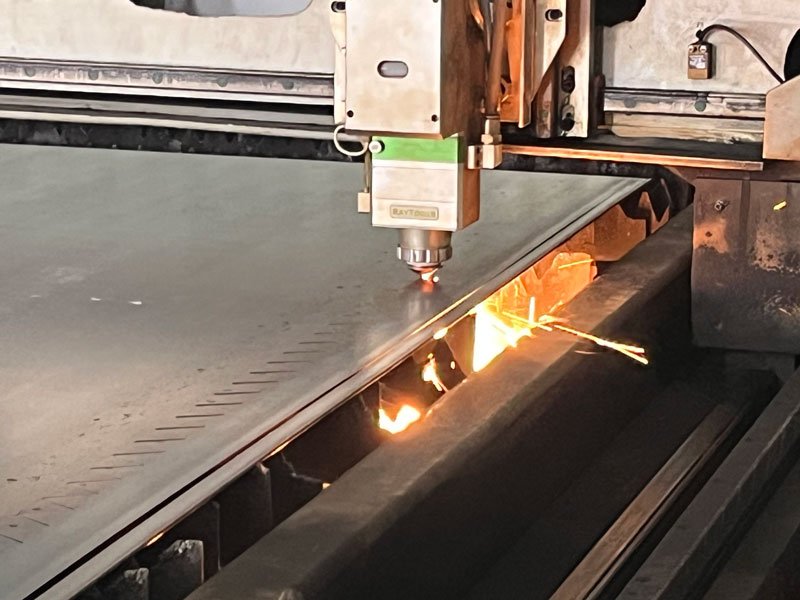
How to Choose a Fiber Laser Cutting Machine for Elevator Manufacturing
Laser Power:
The power of the laser is critical as it determines the thickness of the material that can be cut. For elevator components, use a laser power range of 1000W to 8000W. Higher powers can cut thicker materials, up to 22mm for carbon steel and 16mm for stainless steel1.
Cutting Speed:
Evaluate the maximum cutting speed of the machine. Some machines have speeds of up to 80m/min, which can increase productivity by reducing cycle times.
Material Compatibility:
Ensure the machine can cut the wide range of materials used in elevator manufacturing, including stainless steel, carbon steel, aluminum alloys, and brass. The ability to handle varying thicknesses (from 0.5mm to 28mm).
Precision and Accuracy:
Look for a machine with high positioning accuracy (±0.03mm) and repositioning accuracy (±0.02mm). This ensures that the parts fit correctly during assembly, which is critical in elevator construction.
Work Area:
The size of the cutting area should be adapted to the size of the elevator component being manufactured. Common sizes include 3000mm x 1500mm, but customization may be available depending on specific needs.
Automation Features:
Consider machines with intelligent CNC systems that support a variety of graphic file formats and can automatically adjust cutting parameters based on material type and thickness. This improves operational efficiency and reduces manual intervention.
Maintenance and Support:
Check for after-sales support, including installation, training, and maintenance services. A reliable manufacturer will provide comprehensive support to ensure smooth operation after purchase.
Safety Features:
In a manufacturing environment, safety is paramount. Look for machines with safety enclosures, emergency stop features, and appropriate ventilation systems to manage fumes generated during the cutting process.
Cost Efficiency:
While the initial investment is important, consider long-term operating costs, energy consumption, maintenance requirements, and potential downtime.
Conclusion
Choosing the right fiber laser cutting machine for elevator manufacturing involves balancing power, speed, precision, material compatibility, and support services. By carefully evaluating these factors, manufacturers can enhance productivity, reduce waste, and ensure high-quality production of elevator components.