Laser welding technology has become a revolutionary technology in the rapidly evolving world of manufacturing. Whether you are in the automotive, aerospace, electronics or metalworking industries, understanding laser welding can significantly improve your production efficiency and product quality.
The rapid development of the laser welding market, in the face of a large number of product models, for entry-level welding enthusiasts, this is a difficult problem, “what is laser welding systems”, “How much does a laser welding machine cost” , “laser welding applications “, etc. This article takes you in-depth understanding of the world of laser welding.
This article will take a closer look at what laser welding is, how it works, its benefits, and why you should consider using it in your business. If you are not familiar with this advanced welding technology, you have come to the right place. Why you should consider using it for your business.
What is laser welding machine
Laser welding is a process where a laser beam is used to join two pieces of material—most commonly metals or thermoplastics—by melting the areas that need to be joined together. The laser beam produces high-intensity light, which is focused on a small area to create enough heat to fuse materials together.
Unlike traditional welding, which involves using a filler material or an electric arc, laser welding offers precise, high-speed, and high-quality welds. This makes it especially suitable for industries where accuracy, strength, and aesthetic quality are critical.
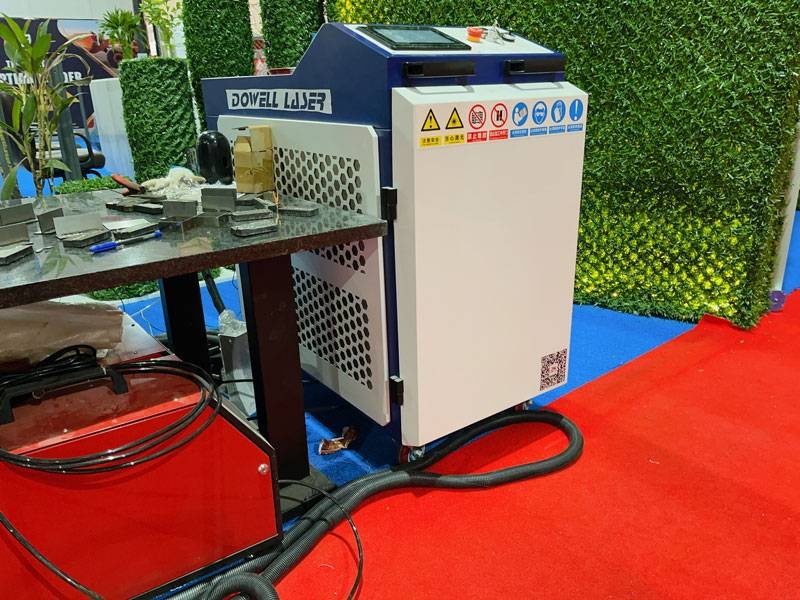
How Does Laser Welding Work?
Laser welding tool works by emitting a concentrated laser beam that can be accurately controlled in terms of its intensity, location, and duration. The beam melts the edges of the materials to be welded, and as it cools, the material solidifies to create a strong joint.
Two methods of laser welding:
Heat Conduction Welding: In this method, the laser beam is absorbed by the material’s surface, causing it to melt. The molten metal then flows together to form a weld. This is ideal for thin materials and produces smooth, aesthetically pleasing welds.
Deep Penetration Welding: For thicker materials, deep penetration welding (also known as keyhole welding) is used. The laser beam vaporizes a small portion of the material, creating a cavity or “keyhole.” This allows the laser to penetrate deeper into the material, forming a strong, deep weld.
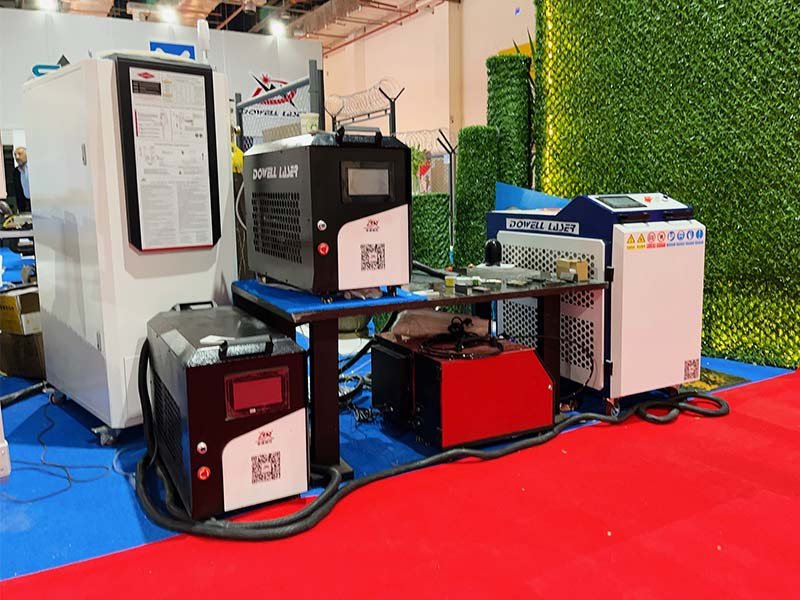
Components of Laser Welding Systems
Laser Source:
- This is the heart of the system. It generates the high-intensity laser beam. Different types of laser sources are available, such as fiber lasers, CO₂ lasers, and Nd:YAG lasers. Each has its own characteristics in terms of wavelength, power output, and suitability for different materials and applications.
Optical Delivery System:
- Beam Delivery Optics: These components guide and focus the laser beam onto the workpiece. They may include mirrors, lenses, and fiber optic cables. The quality of these optics is crucial for achieving a precise and focused beam.
- Beam Shaping Optics: In some cases, the laser beam may need to be shaped or modified to meet specific welding requirements. This can be done using diffractive optics or other beam shaping devices.
Welding Head:
- The welding head holds the optics and is responsible for directing the laser beam onto the workpiece at the correct angle and distance. It may also include features such as gas nozzles for shielding the weld area.
- Some welding heads are designed for manual operation, while others are integrated into robotic or automated systems for precise and repeatable welding.
Control System:
- The control system manages the operation of the laser welding system. It controls parameters such as laser power, beam focus, welding speed, and gas flow.
- It may also include safety features to protect operators and equipment, such as interlocks and emergency stop buttons.
Workpiece Handling System:
- Depending on the application, a workpiece handling system may be required to position and move the workpieces during welding. This can include fixtures, conveyors, or robotic arms.
- The handling system must be designed to ensure accurate positioning of the workpieces and to maintain stability during the welding process.
Gas Supply System:
- Some laser welding processes require a gas supply to shield the weld area from atmospheric contamination. The gas supply system provides the appropriate gas, such as argon or helium, at the correct flow rate.
- The gas nozzle in the welding head directs the gas onto the weld area to protect the molten metal and improve weld quality.
Advantages of Laser Welding
1. Precision
Lazer welding allows for pinpoint accuracy, meaning even small and intricate parts can be welded with minimal distortion. This is especially important for industries like electronics and aerospace, where precision is critical.
2. High-Speed Processing
Laser welding operates at a much faster pace than conventional methods, significantly reducing production time. The high speed is particularly beneficial in high-volume manufacturing environments, such as the automotive industry.
3. Minimal Heat-Affected Zone
Since the laser beam is focused on a small area, the surrounding material is exposed to less heat, which reduces the risk of warping or damage to sensitive parts. This is crucial for delicate materials or components that must maintain strict tolerances.
4. Versatility in Materials
Laser welding can be used on a wide range of materials, including stainless steel, carbon steel, aluminum, titanium, and even plastics. This versatility makes it suitable for a variety of applications, from metal fabrication to medical device manufacturing.
5. Non-Contact Process
Welding laser machine is a non-contact process, meaning there is no physical force applied to the workpiece. This reduces the wear and tear on both the material and the machine, resulting in longer equipment life and lower maintenance costs.
6. Aesthetic Welds
Laser welding often produces clean, smooth welds that require little to no post-processing. This is particularly beneficial for products where appearance is important, such as consumer electronics or medical devices.
Disadvantages of laser welding
1. High Initial Investment
The upfront cost of purchasing a laser welding machine is significantly higher than traditional welding equipment. However, the long-term benefits, such as reduced labor costs and increased efficiency, often offset this investment.
2. Limited Material Thickness
Laser welding is typically more effective on thin to moderately thick materials. For very thick materials, other welding methods, such as arc welding, may be more appropriate.
3. Training Requirements
Due to the complexity of the technology, operators need specialized training to effectively use and maintain laser welding equipment. This may require an initial time and cost investment.

Laser Welding Applications
1. Automotive Industry
Laser welding is widely used in the automotive industry for welding car bodies, exhaust systems, and battery components. Its high-speed processing and precision make it ideal for mass production.
2. Aerospace
In aerospace, laser welding is used to join complex components that require high precision and strength, such as turbine blades and engine parts.
3. Electronics
The electronics industry uses laser welding for assembling tiny components with high accuracy. This is essential for producing devices like smartphones, laptops, and other consumer electronics.
4. Medical Devices
Laser welding is perfect for creating small, precise welds on medical devices, such as surgical instruments and implants. The non-contact nature of laser welding reduces the risk of contamination, making it ideal for the medical field.
5. Jewelry and Watchmaking
In industries like jewelry and watchmaking, where fine details are crucial, laser welding provides smooth, aesthetically pleasing welds that maintain the structural integrity of precious metals.
Why Should You Consider Laser Welding?
Improved Product Quality: Laser welding produces clean, high-quality welds with minimal distortion, improving the overall quality of your products.
Increased Productivity: The high-speed nature of laser welding means you can produce more in less time, increasing your overall output without sacrificing quality.
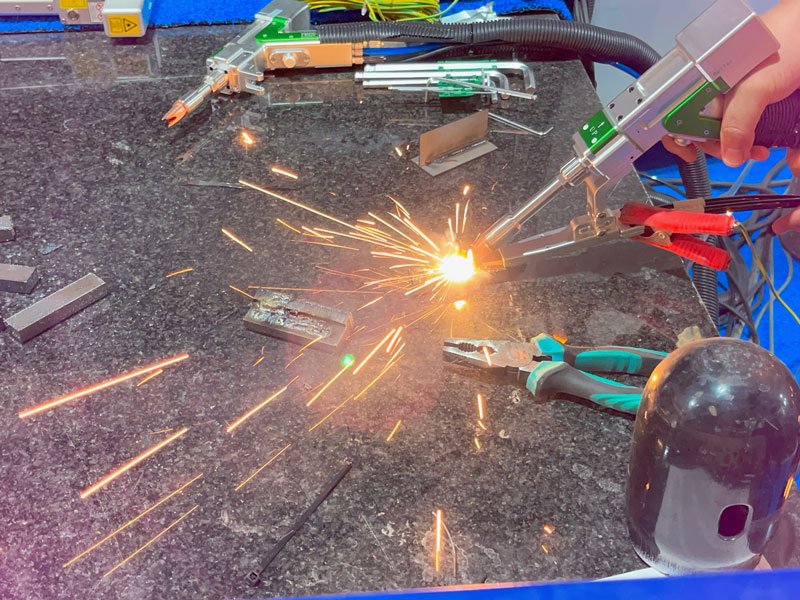
Conclusion
Laser welding is a powerful technology that offers precision, speed, and flexibility for a wide range of applications. Whether you’re looking to improve the quality of your products, reduce production time, or lower operating costs, investing in a laser welding machine could be the next step for your business.
By understanding what laser welding is and how it works, you’re better equipped to make an informed decision on whether it’s the right solution for your needs. If you have any more questions about laser welding or need assistance in choosing the right machine, feel free to contact us!